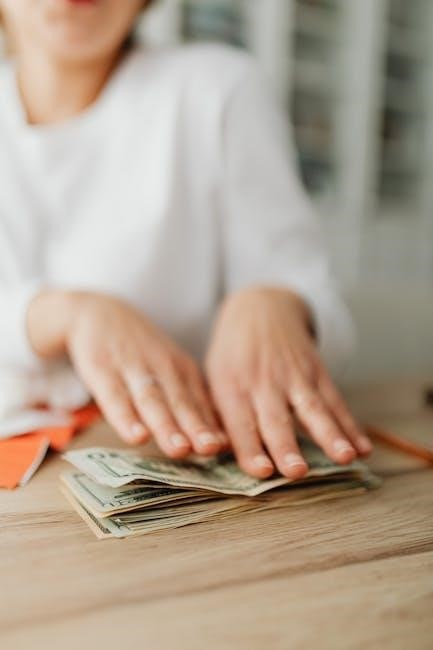
Quality control is a cornerstone of manufacturing, ensuring products meet specified standards. It involves systematic processes to maintain excellence, reliability, and customer satisfaction, forming the foundation of brand loyalty and trust.
1.1 Overview of Quality Control
Quality control involves systematic processes to ensure products meet predefined standards. It encompasses monitoring, testing, and documenting across production stages. Inspectors play a crucial role in identifying defects, ensuring compliance, and maintaining consistency. This process is essential for upholding product integrity, safety, and customer satisfaction, forming the backbone of organizational excellence and reliability.
1.2 Importance of Quality Control in Manufacturing
Quality control is vital in manufacturing as it ensures products meet safety and quality standards, reducing defects and waste. It enhances customer satisfaction, builds brand reputation, and minimizes legal risks. By implementing QC processes, manufacturers can improve efficiency, lower costs, and maintain competitiveness in the global market, ensuring long-term success and reliability.
Roles and Responsibilities in Quality Control
Quality control involves multiple roles, each contributing to ensuring product excellence. From inspectors to managers, these positions collaborate to maintain standards, detect defects, and optimize processes for consistent quality and compliance.
2.1 Quality Control Manager
The Quality Control Manager oversees the entire quality control process, defining standards, developing QC plans, and ensuring compliance. They manage teams, analyze data for improvements, and communicate quality expectations across departments, playing a crucial role in maintaining product excellence and operational efficiency.
2.2 Quality Control Inspector
The Quality Control Inspector ensures product quality by conducting thorough inspections of raw materials, in-process goods, and finished products. They identify defects, document findings, and collaborate with production teams to address issues, maintaining compliance with industry standards and improving overall manufacturing efficiency and product safety.
2.3 Quality Control Engineer
The Quality Control Engineer designs and implements quality processes, ensuring products meet specifications. They analyze data, identify defects, and develop corrective actions. This role requires technical expertise to optimize manufacturing processes, collaborate with R&D and production teams, and ensure compliance with industry standards, ultimately enhancing product quality, efficiency, and customer satisfaction.
2.4 Quality Control Analyst
The Quality Control Analyst monitors and evaluates quality processes, ensuring compliance with standards. They collect and analyze data to identify trends and anomalies, preparing detailed reports to guide improvements. This role involves conducting audits, investigating defects, and recommending corrective actions to enhance product quality and operational efficiency, leveraging analytical skills to support informed decision-making.
2.5 Quality Control Officer
The Quality Control Officer ensures products meet quality and safety standards by monitoring production processes. They enforce systems like HACCP and ISO, document inspection results, and collaborate with teams to identify and resolve quality issues. This role involves maintaining inspection tools, implementing corrective actions, and ensuring compliance with regulatory requirements to guarantee product excellence and consumer safety.
Key Skills and Qualifications for Quality Control Roles
Quality control roles require a blend of education, technical skills, and hands-on experience to ensure product excellence and process efficiency, fostering a culture of continuous improvement and accuracy.
3.1 Education and Certifications
Quality control roles typically require a high school diploma, with preference for certifications like Six Sigma or ISO 9001. Relevant coursework in quality management, engineering, or related fields enhances credentials. Advanced degrees or specialized training in quality assurance can also be beneficial, demonstrating expertise and commitment to industry standards and best practices in ensuring product excellence and process efficiency.
3.2 Essential Skills for Quality Control Professionals
Quality control professionals require strong attention to detail, analytical skills, and problem-solving abilities. Effective communication, proficiency in using precision tools, and knowledge of industry standards are crucial. They must also demonstrate organizational skills, adaptability, and a commitment to continuous improvement to ensure high-quality products and processes, meeting regulatory and customer expectations consistently.
The Importance of Quality Control in Ensuring Product Quality
Quality control ensures products meet defined standards, preventing defects, ensuring safety, and meeting customer expectations, thereby safeguarding brand reputation and fostering customer satisfaction and loyalty.
4.1 Benefits of Implementing Quality Control Processes
Implementing quality control processes ensures defect reduction, improves operational efficiency, and enhances customer satisfaction. It minimizes waste, lowers costs, and ensures compliance with industry standards. By identifying issues early, quality control prevents costly rework, boosts product reliability, and strengthens brand reputation. Effective quality control fosters continuous improvement, ensuring products consistently meet or exceed customer expectations and regulatory requirements.
4.2 Impact on Customer Satisfaction and Brand Reputation
Quality control directly influences customer satisfaction by delivering consistent, reliable products. Satisfied customers foster loyalty, positive reviews, and repeat business. Conversely, poor quality can damage brand reputation, leading to loss of trust and market share. Effective quality control ensures products meet expectations, safeguarding brand integrity and enhancing long-term customer relationships and business success.
Tools and Techniques Used in Quality Control
Quality control utilizes tools like Statistical Process Control (SPC), Total Quality Management (TQM), Six Sigma, checklists, and control charts to monitor and enhance production processes, ensuring high product quality.
5.1 Statistical Process Control (SPC)
Statistical Process Control (SPC) is a method used to monitor and control processes through statistical methods. It ensures product quality by identifying variations and defects early, enabling corrective actions. SPC tools, like control charts, help maintain process stability, reduce waste, and optimize production efficiency, ensuring consistent compliance with quality standards and customer expectations.
5.2 Total Quality Management (TQM)
Total Quality Management (TQM) is a holistic approach to quality management that integrates all departments and functions within an organization. It focuses on customer satisfaction and continuous improvement, utilizing data-driven decisions to enhance product quality. By engaging all employees, TQM fosters a culture of quality, reducing waste, and improving overall operational efficiency to meet customer expectations effectively.
5.3 Six Sigma Methodology
Six Sigma is a data-driven approach to quality management, aiming to reduce process defects below 3.4 per million opportunities. It uses the DMAIC framework (Define, Measure, Analyze, Improve, Control) to identify and eliminate defects. By leveraging statistical tools and methodologies, Six Sigma enhances process efficiency, customer satisfaction, and operational excellence, ensuring high-quality outputs through continuous improvement.
Challenges in Quality Control
Quality control faces challenges like maintaining consistent standards, detecting defects early, and managing documentation. These issues require innovative solutions to ensure product reliability and compliance with regulations.
6.1 Common Challenges Faced by Quality Control Teams
Quality control teams often face challenges such as maintaining consistent standards, detecting defects early, and managing detailed documentation. Additionally, resource constraints, cross-functional collaboration, and evolving regulatory requirements can complicate the process, requiring teams to adapt and innovate to ensure compliance and product reliability while balancing efficiency and accuracy in their operations.
6.2 Strategies to Overcome Quality Control Challenges
To address quality control challenges, teams can adopt robust training programs, leverage advanced technologies like AI and automation, and implement continuous improvement practices. Enhancing cross-departmental collaboration, investing in precise measurement tools, and fostering a culture of accountability also help mitigate issues. Regular audits and feedback loops further ensure sustained compliance and operational efficiency, driving consistent product excellence and customer satisfaction.
Best Practices for Effective Quality Control
Implementing standardized protocols, investing in employee training, and utilizing advanced technologies are key best practices. Regular audits, clear communication, and continuous improvement foster a robust quality control framework.
7.1 Continuous Improvement Practices
Continuous improvement practices involve regularly analyzing and refining processes to enhance efficiency and product quality. By fostering a culture of ongoing learning and adaptation, organizations can identify and address inefficiencies, reduce waste, and maintain high standards. Implementing feedback loops, conducting root cause analysis, and encouraging employee contributions are essential for sustaining growth and excellence in quality control.
7.2 Regular Audits and Inspections
Regular audits and inspections are vital for ensuring compliance with quality standards and identifying discrepancies. These systematic evaluations assess processes, products, and documentation to verify adherence to regulations and internal protocols. By conducting audits, organizations can address issues promptly, improve compliance, and maintain customer trust. Tools like checklists and reports aid in documenting findings for corrective actions and continuous improvement.
Industry-Specific Quality Control Applications
Quality control practices vary across industries, with tailored approaches for manufacturing, food safety, and more, ensuring compliance and maintaining high standards specific to each sector;
8.1 Quality Control in Manufacturing
Quality control in manufacturing is critical for ensuring product excellence. It involves monitoring raw materials, production processes, and final goods to meet standards. Techniques like SPC and TQM are applied to detect defects early, preventing costly rework. By maintaining strict quality benchmarks, manufacturing firms ensure reliability, safety, and customer satisfaction, fostering trust and loyalty in their products.
8.2 Quality Control in Food and Beverage Industry
Quality control in the food and beverage industry ensures safety, compliance, and consistency. Inspectors monitor production lines, test samples, and verify adherence to HACCP, GMPs, and ISO standards. They detect contaminants, check labeling accuracy, and ensure hygienic practices. Proper quality control prevents recalls, protects consumer health, and maintains brand reputation, while complying with regulatory requirements and industry standards.
The Future of Quality Control
The future of quality control lies in advanced technologies like AI, automation, and big data analytics. These innovations enhance efficiency, accuracy, and product consistency.
9.1 Emerging Trends in Quality Control
Emerging trends in quality control include the adoption of AI, automation, and big data analytics. These technologies enhance predictive maintenance, real-time monitoring, and defect detection. IoT devices enable seamless data collection, while machine learning optimizes quality processes. Additionally, the rise of Industry 4.0 and smart manufacturing is driving more integrated and efficient quality control systems, ensuring higher precision and faster issue resolution.
9.2 Role of Technology in Advancing Quality Control
Technology is revolutionizing quality control by enabling real-time monitoring, automated inspections, and data-driven decision-making. AI and machine learning detect defects with precision, while IoT devices collect data across production lines. Advanced software streamlines compliance tracking, reducing human error. These tools enhance efficiency, consistency, and accuracy, allowing organizations to maintain higher standards and adapt to evolving industry demands effectively.
Quality control roles are essential for maintaining product excellence and company success. Their dedication ensures consistency, safety, and customer satisfaction, making them vital to organizational growth and reputation.
10.1 Summary of Key Points
Quality control roles are vital for ensuring product excellence and organizational success. Key responsibilities include monitoring production, testing products, and implementing standards. Effective quality control enhances customer satisfaction, reduces defects, and improves efficiency. Roles such as inspectors, managers, and engineers work collaboratively to maintain high standards, ensuring compliance and driving continuous improvement across industries.
10.2 Final Thoughts on the Importance of Quality Control
Quality control is essential for building trust, ensuring reliability, and fostering customer satisfaction. It protects brand reputation by maintaining consistent excellence and compliance with standards. By preventing defects and reducing waste, quality control enhances efficiency and profitability. As industries evolve, investing in robust quality control processes remains vital for long-term success and competitiveness in an ever-changing market landscape.