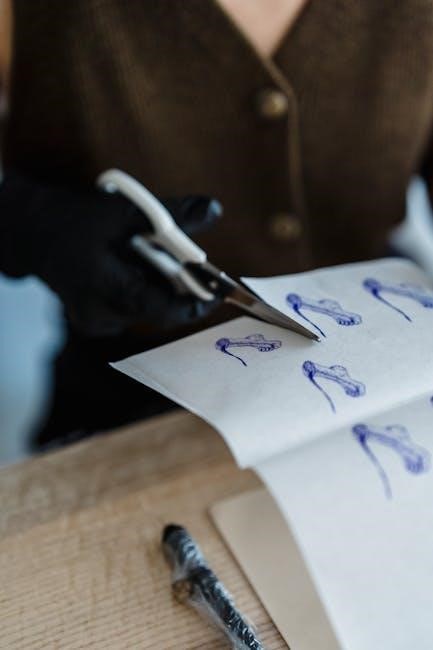
A manual scissor lift is a portable, hydraulic-powered platform designed to elevate personnel, tools, and materials to required heights safely and efficiently, emphasizing operator safety and versatility․
1․1 What is a Manual Scissor Lift?
A manual scissor lift is a portable, hydraulic-powered lifting device designed to elevate personnel, tools, and materials to required heights․ It operates via a hand crank or foot pump, offering a cost-effective solution for industrial, construction, and warehouse applications․ The lift features a scissor-like mechanism that expands and contracts to raise or lower the platform․ Designed for safety and efficiency, manual scissor lifts are ideal for tasks requiring precise height adjustment, such as maintenance, inventory management, and construction work․ Their portability and ease of use make them a versatile tool in various work environments․
1;2 Basic Functionality and Purpose
The basic functionality of a manual scissor lift revolves around its ability to safely elevate loads to desired heights using a hydraulic system activated by a hand crank or foot pump․ Its primary purpose is to provide a stable and secure platform for workers, tools, and materials in various environments․ Designed for versatility, manual scissor lifts are used in industrial settings for maintenance, construction sites for elevated tasks, and warehouses for inventory management․ They offer a reliable, low-maintenance solution for lifting needs, ensuring productivity and safety without the requirement for complex electrical systems, making them ideal for both indoor and outdoor applications․
Design and Components of Manual Scissor Lifts
Manual scissor lifts feature a scissor mechanism, hydraulic system, and a sturdy platform, designed for safe and efficient lifting with manual operation and essential safety features․
2․1 Scissor Mechanism and Hydraulic System
The scissor mechanism consists of linked, folding arms that provide stability and lift․ The hydraulic system, operated manually via foot pumps or hand cranks, ensures smooth elevation and lowering, enabling precise control for various tasks while maintaining safety and efficiency in industrial and construction settings․ This design allows the lift to handle different load capacities effectively, making it versatile for multiple applications․ Proper maintenance of the hydraulic system is crucial for optimal performance and longevity of the equipment․ Regular checks and services ensure reliable operation and prevent potential malfunctions․ Operators must adhere to manufacturer guidelines to maintain system integrity and safety standards․
2․2 Platform and Load Capacity
The platform of a manual scissor lift is designed for durability and stability, typically constructed from robust materials to support varying load capacities․ Load capacities range from a few hundred kilograms to several tons, depending on the model and application․ The platform size varies to accommodate different tasks, ensuring safe and efficient operation․ Safety features, such as non-slip surfaces and guardrails, enhance worker protection․ Load capacity ratings are clearly specified by manufacturers to prevent overloading, ensuring safe and reliable performance across industrial, construction, and specialized environments․ Adherence to these specifications is critical to maintain stability and prevent accidents during operation․
2․3 Manual Operation Features (Foot Pump, Hand Crank)
Manual scissor lifts are equipped with user-friendly operation features, including foot pumps and hand cranks, designed for easy and efficient height adjustment․ The foot pump allows operators to raise the platform by depressing the pedal, while the hand crank provides an alternative method for precise control․ These manual mechanisms ensure smooth lifting and lowering, even in environments without power access․ The systems are designed for minimal effort, reducing operator fatigue during prolonged use․ Safety features, such as pressure relief valves, prevent overloading and ensure stable operation․ These manual controls are ideal for applications requiring precise height adjustment and reliable performance in various industrial and construction settings․
2․4 Safety Mechanisms and Emergency Stops
Manual scissor lifts incorporate essential safety mechanisms to ensure operator protection․ Emergency stop systems, including push-button controls and manual overrides, allow immediate halting of operations in critical situations․ These lifts are equipped with safety valves to prevent sudden drops and ensure controlled descent․ Pressure relief mechanisms safeguard against overloading, while panic stops instantly deactivate all functions․ These features comply with industry standards, prioritizing user safety and equipment stability․ Regular maintenance of these systems is crucial to ensure reliability and performance, providing a secure working environment for operators across various applications․
Operating Instructions for Manual Scissor Lifts
Operating a manual scissor lift involves pre-operation checks, controlled lifting, and movement on level surfaces to ensure safe and efficient use, following operational guidelines․
3․1 Pre-Operation Checks and Preparation
Before using a manual scissor lift, ensure all safety measures are in place․ Always read and understand the operator’s manual thoroughly․ Conduct a visual inspection of the hydraulic system, scissor arms, and platform for any signs of wear or damage․ Check the oil levels and ensure the foot pump or hand crank operates smoothly․ Clear the surrounding area of obstacles and ensure the surface is flat and level․ Test the emergency stop mechanism to confirm it functions properly․ Wear appropriate safety gear, such as hard hats and harnesses, and ensure the load does not exceed the specified capacity․ Never operate the lift without proper training or authorization․
3․2 Lifting and Lowering Procedures
Operate the manual scissor lift smoothly and cautiously․ Begin by ensuring the platform is clear of obstructions and the area is free from hazards․ Use the foot pump or hand crank to lift the platform gradually, maintaining control throughout the process․ Always keep hands and arms away from the scissor arms during movement․ When lowering, ensure the platform descends evenly and avoid sudden stops․ Check for overhead obstructions and ensure the surface remains level․ Maintain three points of contact while ascending or descending․ Never exceed the load capacity, and ensure the platform is stable before allowing personnel to step on or off․ Proper lifting and lowering techniques are essential for safe operation;
3․3 Moving the Lift on Flat and Level Surfaces
Ensure the surface is flat and level before moving the manual scissor lift․ Clear the area of obstacles to prevent collisions․ Trained operators should handle the movement, ensuring the lift is stable and secure․ Always check the load capacity and ensure it is not exceeded․ Use the designated handles or controls to maneuver the lift smoothly․ Avoid sudden jerks or sharp turns, which could destabilize the platform․ Lower the platform to its lowest position before moving to maintain balance; Ensure all personnel are clear of the lift during relocation․ Adhere to safety guidelines and manufacturer instructions for safe transport on flat surfaces․
Safety Instructions and Warnings
Only trained operators should use the lift․ Ensure proper load capacity and stable surfaces․ Wear PPE and keep limbs clear of moving parts during operation․
4․1 General Safety Rules for Operators
Operators must be trained and authorized to use the lift․ Always read the manual thoroughly before operation․ Ensure the load does not exceed the rated capacity․ Operate only on flat, stable surfaces․ Wear proper PPE, including hard hats and safety harnesses․ Keep loose clothing and jewelry away from moving parts․ Never allow unauthorized individuals to operate the lift․ Maintain clear visibility and avoid overreaching․ Ensure all safety mechanisms are functioning properly before use․ Be aware of overhead obstacles and ensure proper clearance․ Never leave the platform unattended while elevated․ Follow all manufacturer guidelines and safety protocols to prevent accidents․
4․2 Specific Precautions During Operation
Always maintain a safe distance from moving parts, such as scissor arms, to avoid injury․ Ensure the platform is fully lowered before moving the lift․ Never exceed the load capacity specified in the manual․ Keep hands and arms clear of the scissor mechanism during operation․ Avoid sudden movements or jerks while lifting or lowering․ Ensure the surface is flat and level before elevating․ Never lean over the platform edges or overreach․ Use the provided control panels to operate the lift smoothly․ Regularly inspect hydraulic lines for leaks or damage․ Avoid operating near overhead obstructions or power lines․ Secure all tools and materials on the platform to prevent shifting during elevation․
4․3 Emergency Procedures and First Aid
In case of an emergency, stop the lift immediately and secure the area to prevent further incidents․ If someone is injured, do not move them unless there’s immediate danger․ Provide first aid for minor injuries, such as cuts or bruises, and seek professional medical help for serious conditions․ Always follow the lift’s emergency stop procedures and consult the manual for specific guidance․ Ensure the lift is checked for hydraulic leaks or damage before resuming operation․ Regular training and inspections can help prevent emergencies․ Remember, prevention is key, so always adhere to safety guidelines to minimize the risk of accidents․
Maintenance and Troubleshooting
Regular hydraulic system checks and routine maintenance ensure smooth operation and longevity of the manual scissor lift, preventing common issues and enhancing workplace safety standards․
5․1 Daily and Weekly Maintenance Checks
Daily checks involve inspecting hydraulic fluid levels, ensuring proper lubrication, and verifying the integrity of scissor arms and safety mechanisms․ Weekly maintenance includes thorough cleaning of the platform and controls, checking for hydraulic leaks, and testing emergency stops․ Operators should also review the load capacity and ensure all components are secure․ Regular greasing of moving parts and inspection of wire ropes are essential․ Additionally, verifying the functionality of foot pumps or hand cranks and ensuring proper alignment of the platform during operation are critical․ These routine checks help prevent malfunctions and ensure the lift operates safely and efficiently, adhering to manufacturer guidelines and safety standards․
5․2 Hydraulic System Service and Repair
Regular servicing of the hydraulic system is crucial for maintaining the performance and longevity of the manual scissor lift․ Operators should check hydraulic fluid levels daily and top them up as needed․ Inspect hoses and connections for leaks or damage, replacing worn components promptly․ When repairing, ensure the lift is on a level surface and the platform is fully lowered․ Follow the manufacturer’s guidelines for replacing hydraulic seals or pumps․ Always refer to the service manual for detailed repair procedures․ Proper maintenance prevents hydraulic failure, ensuring smooth and safe operation․ Neglecting these steps can lead to system malfunction, posing safety risks to operators and materials․
5․3 Common Issues and Solutions
Common issues with manual scissor lifts include hydraulic fluid leaks, uneven platform lowering, and malfunctioning safety mechanisms․ For fluid leaks, inspect hoses and connections, tightening or replacing them as needed․ If the platform lowers unevenly, check for obstructions or misaligned scissor arms and ensure proper lubrication․ Safety mechanisms failing to engage may require resetting or replacing sensors․ Always consult the service manual for detailed repair steps․ Addressing these issues promptly ensures reliable operation and prevents potential accidents․ Regular maintenance can help mitigate these problems, extending the lifespan of the lift and maintaining workplace safety standards․
Applications of Manual Scissor Lifts
Manual scissor lifts are widely used in industries like manufacturing, construction, and warehouses for elevating personnel, tools, and materials to high areas efficiently and safely․
6․1 Industrial and Warehouse Use
Manual scissor lifts are essential in industrial and warehouse settings for tasks requiring elevation, such as inventory management, equipment maintenance, and material handling․ Their compact design allows easy navigation through tight spaces, making them ideal for facilities with limited clearance․ The lifts enable workers to access high shelves, perform repairs, and transport goods efficiently․ With their durable construction and reliable hydraulic systems, these lifts enhance productivity while ensuring operator safety․ They are often used in conjunction with other material handling equipment to streamline operations and reduce downtime, proving indispensable in fast-paced industrial environments․
6․2 Construction and Outdoor Applications
Manual scissor lifts are widely used in construction and outdoor settings due to their versatility and durability․ These lifts are ideal for tasks such as repairing structures, installing equipment, and accessing high areas on uneven terrain․ Their robust design allows them to operate effectively in rugged environments, making them a preferred choice for construction sites, landscaping projects, and outdoor event setups․ Portable and easy to maneuver, manual scissor lifts enable workers to complete tasks efficiently while maintaining safety standards․ They are also used for temporary access solutions in remote locations where traditional lifts may not be feasible, ensuring productivity in diverse outdoor conditions․
6․3 Specialized Models for Specific Tasks
Specialized manual scissor lifts cater to unique requirements, offering tailored solutions for specific industries․ For instance, low-profile models are designed for vehicle maintenance, enabling easy access under cars and trucks․ Narrow-width lifts are ideal for confined spaces like aisles or tight corridors․ Additionally, models with extended platforms or higher load capacities are available for tasks requiring more space or heavier equipment․ Some lifts feature adjustable deck sizes or customizable attachments, allowing adaptation to specialized jobs․ These tailored designs ensure that users can address specific challenges efficiently while maintaining safety and operational performance, making manual scissor lifts versatile tools across various specialized applications and environments․